News
A simulation of a nuclear facility makes it safer to upgrade waste handling robots
21 July 2025
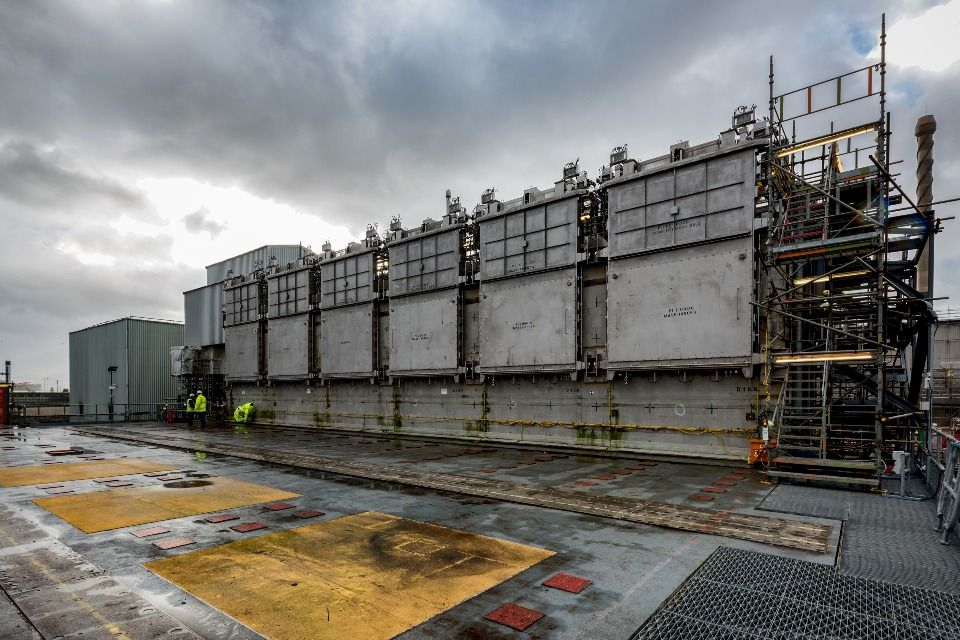
Sellafield’s Pile Fuel Cladding Silo (PFCS) is a legacy waste storage facility and priority for decommissioning on the site. It was originally built in the 1950s to store radioactive cladding from the nuclear fuel used by the very first reactors on the Sellafield site. Today, it is one of the most hazardous facilities on the site and needs to be emptied so the waste can be repackaged into safe, modern storage. Within the silo is a Waste Container Handling Facility, a concrete room where robots process waste containers.
One such robot is a large 6-axis industrial robot arm, which unbolts empty containers, sends them to be filled with waste, then securely bolts the returning containers for onward transfer. The arm also swabs the outside of the container to check for contamination and puts the swab in a deposit box for analysis.
Executing pre-programmed tasks is routine. But when physical upgrades are needed, such as adding new swabbing tools to the robot arm, operators have to take the robot out of service, and suit up in full protective gear to make changes. Changes need multiple test runs, often with several human re-entries to adjust the setup. Each entry creates risks to human health and risk of damaging the robot, whilst trial runs for new setups create downtime. Even pure software upgrades require downtime while the new programme runs on the robot, monitored by cameras and personnel in the facility.
Through the PFCS Operational Simulator (OpSim) project, the RAICo team developed a simulation that allows these changes to tooling or operational procedures to be tested and validated in the simulation before deployment into the facility. Once validated, software updates can be transferred digitally to the robot with almost no downtime, and physical updates need far fewer entries to make changes.
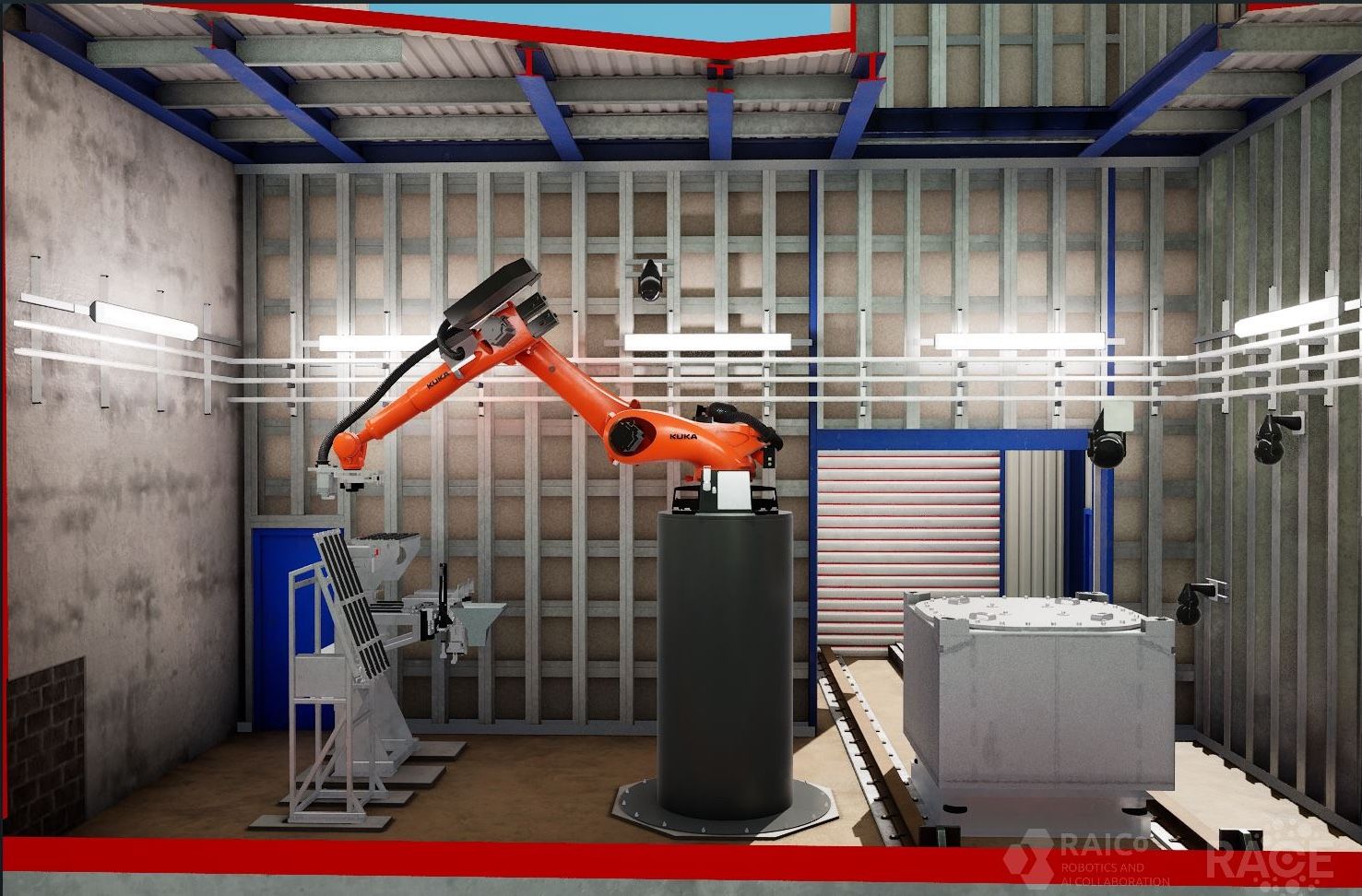
How RAICo and Sellafield Ltd created a simulation of a waste handling facility
This project harnessed cutting-edge robotics, purpose-built 3D software, and a team that combined RAICo and Sellafield Ltd expertise in digital technologies and nuclear decommissioning environments.
To map the waste handling facility, a robotic quadruped, Spot, entered the silo with a LiDAR scanner, which uses lasers to collect precise positional data of everything in the space.
Those data points were converted into 3D CAD assets, which were used to build a precise digital replica of Sellafield’s PFCS. That was done using RAICo’s in-house 3D visualisation software platform, RHOVR (Remote Handling Operations Virtual Reality), which harnesses the Unreal Engine – better known for its use in video games – to create hyper-realistic 3D environments.
Next, an off-the-shelf simulator of the robot’s hardware and software was acquired, and integrated into the RHOVR setup – the most technically challenging element of the project – so the team could run robot programmes in a photorealistic virtual environment.
Finally, the simulator was validated over six months, before being formally demonstrated at RAICo1 in March 2025.
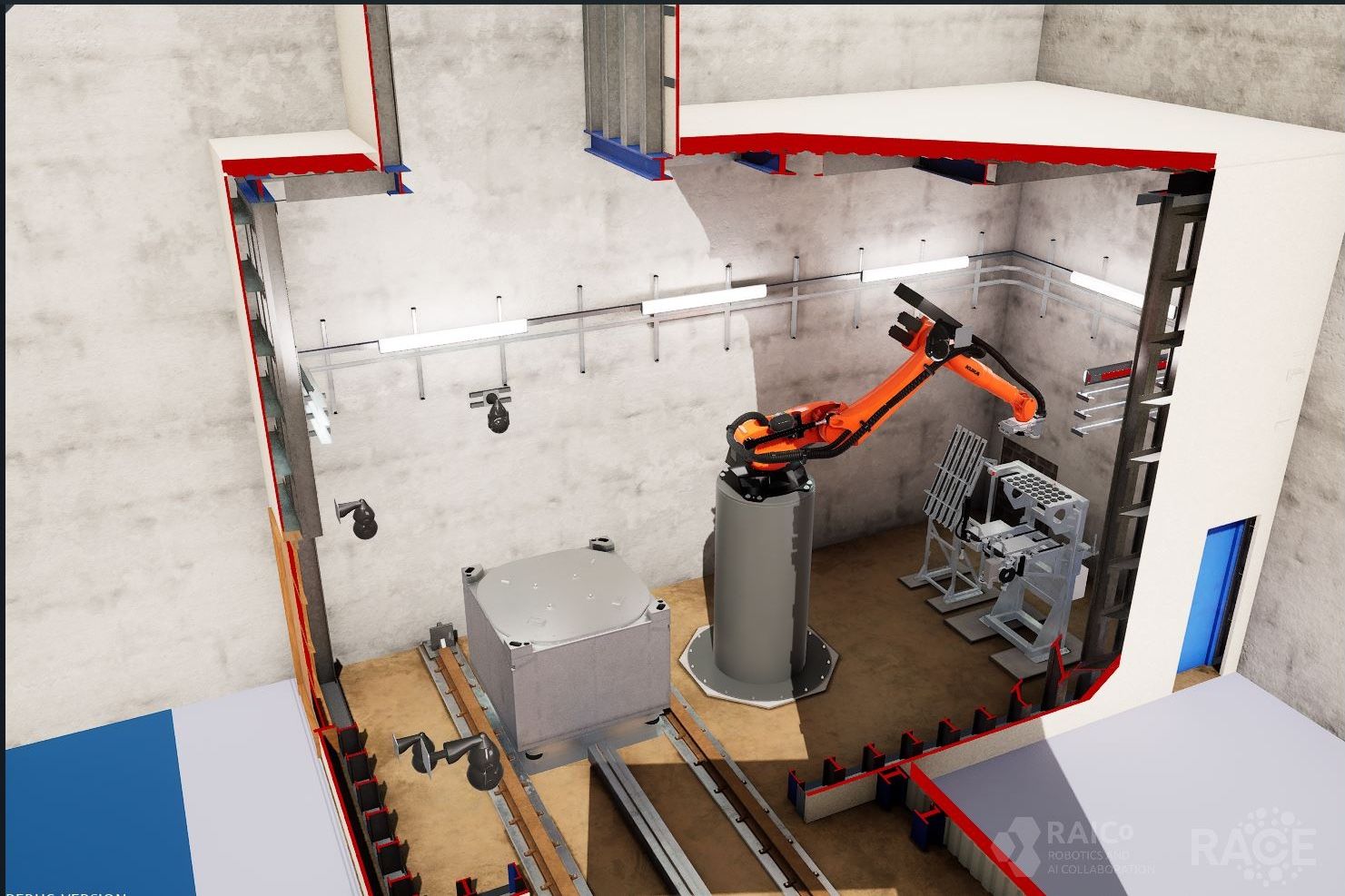
From demonstration to deployment
The demonstration was well-received, and a working version has since been established at Sellafield’s Ltd’s Engineering Centre of Excellence, where it is already being used to execute and verify existing robot programs in the simulation environment, as well as for providing visual demonstrations of how the PFCS facility operates.
This may be just the start. Many Sellafield facilities have similar setups, for example the Waste Transfer Route – the pathway of waste to storage and disposal – uses similar robots in similar sealed rooms for bolting and unbolting waste containers. That opens the door to future projects through the RAICo programme that could adapt the simulator to a wide range of use cases across the Sellafield site.
Rav Chunilal, Head of Robotics and Artificial Intelligence at Sellafield Ltd said: “This collaboration with RAICo has continued to help Sellafield approach complex robotic operations in hazardous environments. By working seamlessly together we’ve developed a simulator that allows us to test and deploy changes virtually, reducing downtime and risk, and making it safer for our operators.”
“It’s accelerating our mission and setting a new benchmark for innovation in nuclear decommissioning which can be repeated across Sellafield and other NDA group operating companies.”
Kate Canning, NDA Head of R&D said “This is a great example of a solution that can be deployed across the NDA group, bringing even greater benefits. It demonstrates the value of NDA group’s participation in the RAICo programme which is accelerating deployment of transformational technologies across our sites and facilities.”
To learn more about the project, or how the innovations behind it could be deployed to other areas of robotics in hazardous environments, contact [email protected]
Contains public sector information licensed under the Open Government Licence v3.0.